Industrial engineering calculations in garment production factory is the most powerful waste quantifying and reduction tool.
These calculations are important because without setting up a target it is highly unlikely that you will be able to achieve what is expected. Once the target is set and we know what is expected we can take steps to achieve the target production. It gives industrial engineers clear picture about the performance of sewing operators, supervisors and the sewing line. The things that an industrial engineer needs to calculate are: capacity, efficiency, performance and utilization.
Knowing I.E terms:
- On standard time – The time spent in doing measured work is called On Standard time example – stitching, bundle handling etc.Any work for which S.A.M has been applied will be On standard.
- Off standard – The time spent in doing unmeasured or non-value adding work is called Off standard time. Example – Machine breakdown, waiting time etc.
- SMV – The time taken by a 100 % rating operator to complete an operation.
- SAM = SMV+ allowances
- Minutes earned – production in terms of time is called as minutes earned. it is calculated by multiplying production with SAM
- Available minutes – The total working hours available for an operator or a group of operators
Capacity
The number of garments a factory is capable to produce is called capacity of factory. Capacity calculation helps in planning of resources. Example:
If the SAM of a shirt is 25 mins, how many of these shirts can a factory, having 200 workers who are working 48 hours a week, produce in a week?
Ans :

Therefore,Capacity = (200*48*60)/25
= 23040 garments in a week
Note : We multiplied by 60 to convert hours into minutes.
Performance, Utilization and Efficiency
-
Performance :
Performance is primarily the Measure of effectiveness of individual operator. It tells how well an individual operator is performing.
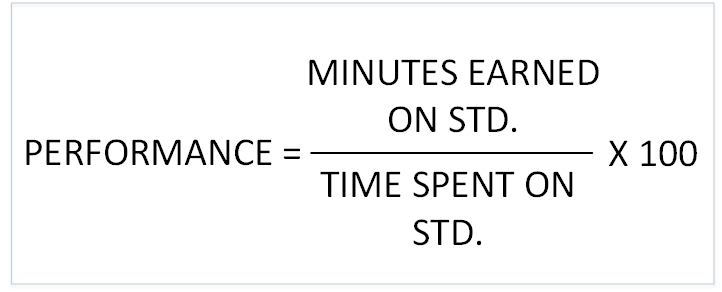
Where ,
Minutes earned on Std. = No. of pieces produced * S.A.M
Time spent on Std = Total available time – total off standard time
Note : We are subtracting total off standard time from total available time because here we are calculating operators performance. Machine breakdown, waiting and other off standard time is not under the control of the operator. Supervisor/manager is responsible for keeping off standard under check.
2. Utilization
Utilization is the measure of how well a supervisor is able to use the operators by keeping the off standard to minimum.
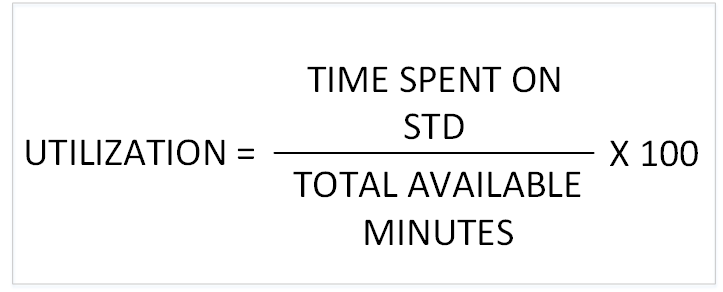
Where,
Time spent on Std. = Total available time – Off Std. time
Total available time = total worked minutes.
Note : Here we are checking the performance of supervisor therefore we will use total available time and divide On standard time by total available time. Main goal here is to find the amount of off standard.
3. Efficiency
Measure of how well the sewing line is run. It is the combined measure of both the performance and Utilization.
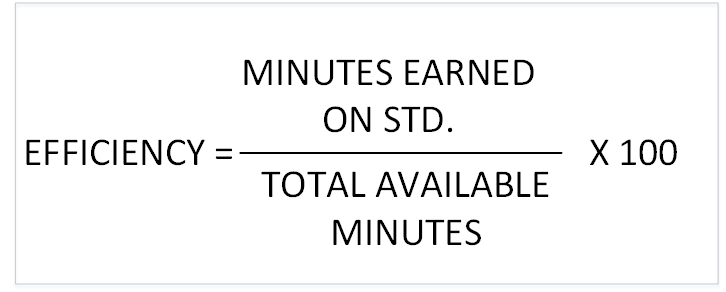
Note : In efficiency calculation we use both the available minutes and Minutes earned by actual production because we want to measure the performance of the complete sewing line. This formula undertakes both the operator and supervisors performance, that is Performance and Utilization in calculation.
Let’s Calculate performance, utilization and efficiency now:
Operator Jay attends, full day/480 minutes, and produces 1000 pieces at SAM of 0.40. He had to wait 50 minutes for work and 10 minutes for machine breakdown. Calculate the operators performance, Utilization and efficiency.
Ans: Standard minutes produced = 1000*0.40 = 400 minutes
Time on standard = 480-(50+10) = 420 minutes
Performance = 400/420 = 95.2%
Operator Utilization = 420/480 = 87.5%
Operator Efficiency = 400/480 = 83.3 %
Here is the excel file template with formula. Download it for recalling the formula quickly and for easy industrial engineering calculations in garment production factory.
this is good for garment manufacturing plant
Yes Gashaw, probably one of the most important aspect of manufacturing.
hi!,I love your writing so so much! proportion we keep up a correspondence more about your post on AOL? I need an expert in this house to solve my problem. Maybe that’s you! Looking ahead to peer you.
Thank you Jonnie. That’d be great. Please write to me on leanstitchtalk@gmail.com
I appreciate, result in I discovered just what I used to be looking for. You have ended my four day lengthy hunt! God Bless you man. Have a great day. Bye
Thank you Peggie. Glad I could help you 🙂
This is such a great post. I am a software developer. You post help me better understand the difference between efficiency and performance. I salute you
Thank you so much Oluwatobi. This means a lot 🙂
Hi,I want to learn about overall IE,can you help me please.
Hi,
I hope that the article helped you in some way. I will try posting more on IE.
Thanks
thanks for giving me clear idea specially on performance and efficiency!!
Actual time=0.22 minute
Observed time=0.20 minute
Then performance rating = observed time/Actual time *100
P.R=0.2÷0.22=0.100=90%
Is it ok and what we mean can respond answer sorry
What is the difference between observed time and actual time???
All good advice and explanations. My only question is use of terms. When I completed my IE qualification (many years ago) standard time was BASIC TIME plus allowances. SMV & SAM did not appear in text books.
Terminology changes
Good changes are all accepted but still there is no consensus on SMV or SAM.